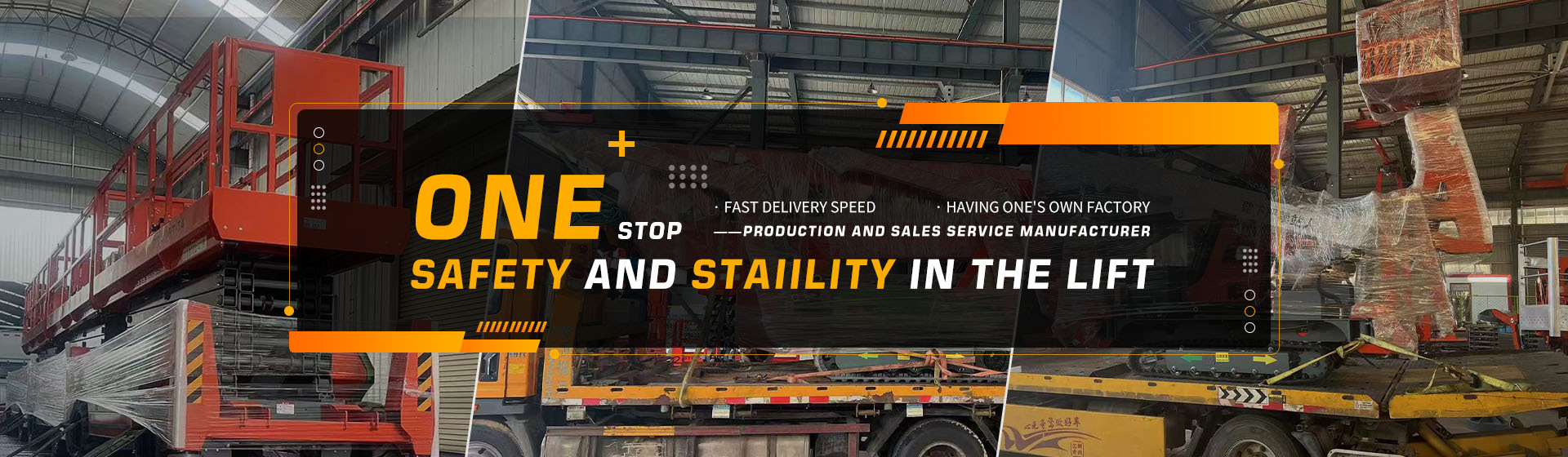
Nearly 20 Chinese leasing companies visited Manitou's French and Italian factories
2023-11-07 08:09As a multi-functional material handling equipment, telescopic arm forklift is widely used in construction, agriculture, industrial fields, in mature markets such as Europe and the United States, more than 50% of the telescopic arm forklift applications are concentrated in the construction industry, and at the same time, the rental market is the most important part of construction applications.
In 2019, Manitou all aspects of Manitou Group from design and raw material control to production process and pre-delivery inspection left a deep impression on the visitors; In order to let more Chinese leasing companies personally experience the production process of Manitong's high-quality products, in October 2023, Manitou once again invited the owners and managers of nearly 20 Chinese leasing companies to visit Manitong's several important telescopic arm forkloading manufacturing plants.
Ancenis Headquarters & Factory, Manitou
The first stop of the delegation arrived at the headquarters of Manitou Group, which is also the largest production site of its 10 manufacturing plants in the world - Ancenis plant.
Mr. Alain Becque, Vice President of Manitou Group Global Key Accounts (Leasing Key Accounts), welcomed the delegation of Chinese leasing companies at Manitou Group's Museum and Customer Experience Center and introduced the history of Manitou Group and its development over 60 years: Since its founder, Mr. Braud, invented the world's first off-road forklift truck in 1958, today Manitou Group is France's largest manufacturer of construction machinery, ranked 24th in the world's TOP 50 list, with revenues of nearly 2.4 billion euros in 2022, and designs and manufactures a full range of telescopic forklifts (2 to 40 tons, 40 tons). 4 m to 35 m), the application covers the construction, agriculture and industrial markets, users in more than 140 countries and regions, accounting for 25% of the global market share.
The Manitou Group Museum displays a restoration of the world's first off-road forklift truck, as well as representative works from various periods of Manitou's history.
Ms. Jacqueline Himsworth, Chairman of the Board of Directors of Manitou Group, also came to the scene to express her welcome to the visit and take a photo with everyone.
In the production workshop of the factory, the delegation got to know every detail of the manufacturing process of Manitou telescopic arm forklift truck up close.As early as 2007, Manitou started using industrial robots to participate in the production of vehicles. From the automatic storage and retrieval of incoming materials of the lifting arm and frame steel plate to the robotic laser cutting and welding, the pursuit of modern high-quality manufacturing has never stopped. Traveling through different manufacturing areas of the factory, the delegation witnessed Manitou's strict control of quality control in the manufacturing process, the precise control of each process and the documentation, so that every piece of equipment delivered to the user can trace the history and records of every link in the manufacturing process.
In the vehicle test site, each factory vehicle is carefully inspected by 240 inspection points, and then the full-time test personnel (who must work in all manufacturing links of the factory for at least 5-10 years) drive the vehicle to complete various performance tests, including the ultimate performance test of the vehicle, the whole process lasts 3-4 hours. At the scene, more than 10 vehicles under test ran back and forth, and the superburning scene also brought the visit to a climax.
Manitou global spare parts logistics center
The Manitou Global Spare Parts Logistics Center is a 10-minute drive from Ancenis Group headquarters. This is a 33,500 square meter Manitou International spare parts logistics center built in 2007 with an investment of 30 million euros. Today, there are more than 240,000 different parts categories here, and about 1 million orders are issued from the spare parts logistics center every year (about 4,000 orders per day). It handles about 40 tons of goods and more than 1,000 parcels every day. 150 people work here in shifts from 5 a.m. to 21 p.m. to ensure that more than 70,000 numbered spare parts can be shipped worldwide within 24 hours.In response to the space constraints of the logistics center, Manitou introduced Mecalux's latest storage and order picking technology from 2021. The new automated storage and retrieval system (AS/RS) allows more than 20,000 storage boxes to be accommodated in 560 square meters of space, coupled with two high-performance picking stations. It can effectively increase the throughput of Manitou Group's nearly 16,000 SKU numbered small, high-turnover parts. Now, with just two operators, this automated storage system can prepare 500 order lines per hour.
Manitou Laillé Factory
Located in Brittany, France, the Laille plant covers an area of 50,00m ², mainly producing Maniton compact telescopic forklifts with lifting heights of 4-6 meters and rated loads of 2-2.5 tons, including MT/MLT 625, MT 420 and MT 415 models.
In the parking area and test area of the equipment, the delegation could not wait to enter the cab and experience the comfortable driving environment, humanized control mode and good vision of the Manitone compact forklift. "Small size, big energy!" The compact forklift is a very large equipment in the European market, and the feeling of close proximity has also brought some inspiration to the elites of the Chinese leasing industry to explore the Chinese market.
French European well-known leasing company Kiloutou
The Kiloutou Group is the second largest general equipment leasing company in France and the third largest in Europe, with 600 subsidiaries, more than 1,000 product types and more than 350,000 sets of equipment (not including accessories). For more than 40 years, we have been combining economic development with environmental and human values to provide the most innovative solutions to an increasingly diverse customer base. At the beginning of 2023, Kiloutou Group and Manitong Group cooperated to jointly research the electric stamp telescopic arm forkloading truck originally designed for diesel power, giving second-hand equipment a second life while reducing carbon emissions.
The delegation visited Kiloutou Nantes Center store, which is also its regional headquarters in the Western French region, responsible for the management of more than 2,000 large equipment, including telescopic arm forkloading, aerial work platforms, generator sets, and more than 100,000 pieces of small equipment. The person in charge of the Nantes center store answered the common questions about the equipment matching, selection, personnel deployment and function setting of the fleet in detail; As well as the number and specifications of the telescopic arm forklift truck that the delegation is most concerned about, as well as the trend of equipment electrification. During the one-and-a-half hour visit, equipment rental colleagues from China benefited a lot and expressed their heartfelt thanks to Kiloutou for its warm reception.
Manitou Italian factory
Manitou Italy - Manitou manufacturing base for rotary and heavy-duty telescopic boom forklifts, including the world's largest telescopic boom forklift MHT14350 (lifting height of 14 meters, rated load of 35 tons).
Manitou Italia is located in the "Motorvalley" of the Emilia-Romagna region in central Italy, surrounded by world-renowned car brands. At the same time, there are also many high-quality vehicle parts suppliers here, providing an important guarantee for Manitou's high-quality products.
Mr. Carlo Razzoli, Marketing Manager, presented the history and corporate profile of Manitou Italy. In order to meet the growing global demand for rotary and heavy-duty telescopic fork loaders, the Manitou Italian plant has also been expanded in recent years and now covers a total area of more than 100,000 square meters and employs more than 700 people.
Entering the production workshop, a material car shuttles back and forth from different stations, busy but orderly. According to the production manager, the original equipment production is divided into 12 stations according to the installation sequence, and the materials required for assembly of each station are delivered by the material truck 2 hours in advance according to the production order of the day. This not only ensures the accuracy of the materials, but also allows assembly workers to focus on assembly operations and improve efficiency. During this period, every production process is documented and archived, ensuring that every step of every piece of equipment delivered to the user can be traced.
Like the French factory, all the equipment produced in the Italian factory is also subject to a variety of stringent factory tests before leaving the factory. At the site, Manitou Italy also specially arranged two new electric and diesel rotary telescopic fork loading models for demonstration and experience.